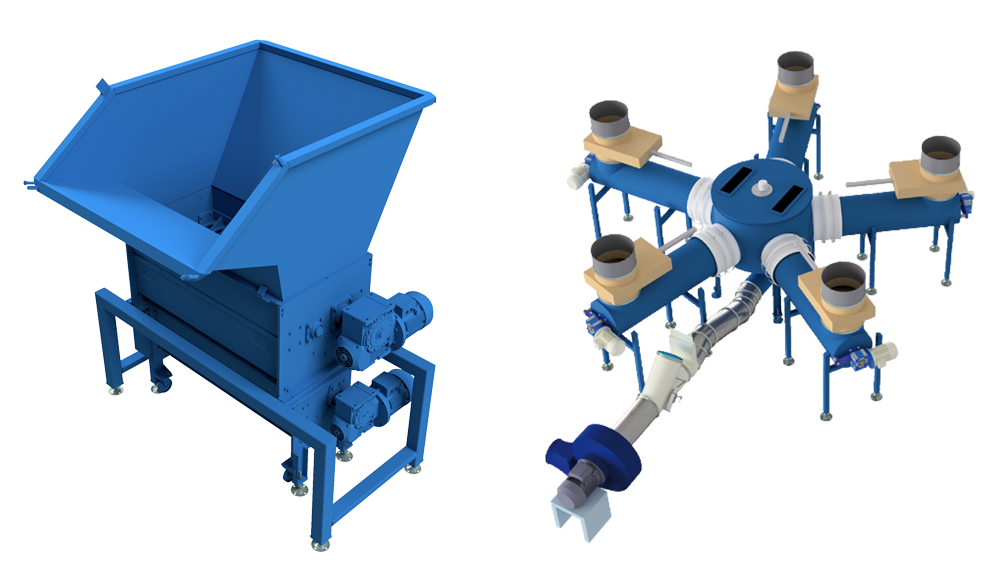
Recycling Equipment for waste of eps
For internal scraps and eps waste collected outside
Allowing to re-use the material (thanks to a proper treatment) in a profitable way
Available in different combinations of capacity within 15 ÷ 100 m³/h (530 ÷ 3,530 ft³/h)
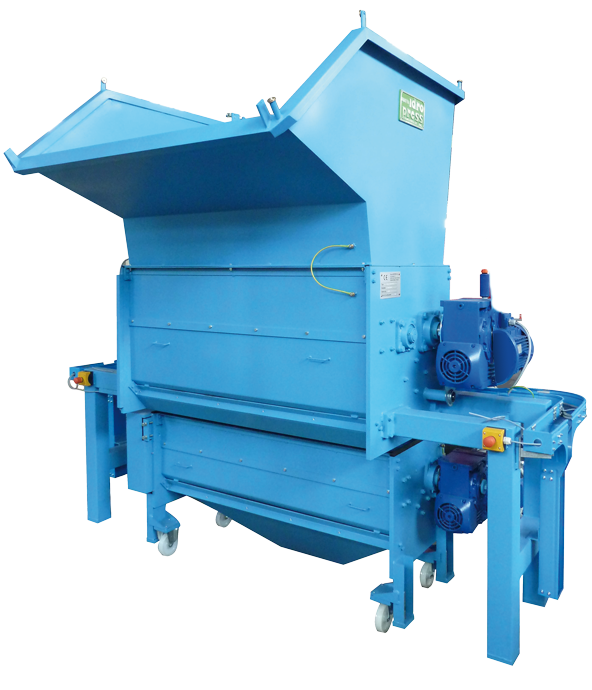
First Step: Crushing
Low revolution speed Pre-crushers & Grinders for low noise and low dust generation. Grinding Fans for further size reduction when necessary to go below 10 ÷ 12 mm (0.39 ÷ 0.47 in) diameters. Suitable for densities within 6 ÷ 80 kg/m³ (0.37 ÷ 5.00 lb/ft³). Possible to complete with automatic feeding conveyor belts for a faster feeding.
Second Step: Dedusting (and Dust Compacting)
Material cleaning from any eventual dust content is a very important passage before recycling the crushed eps waste back to block or shape moulded parts in order to keep the moulding machines clean and therefore in order to ensure proper quality of block and moulded parts containing recycled eps waste.
Dedusting Process can be done both with
- Standalone Machines to be placed (*) after a Grinder or Grinding Fan (*) after a collecting silo for ground waste on the pipeline to moulding machine (block mould or shape mould).
- Integrated Devices installed directly on Mixing Unit in front of block mould or shape mould so that during mixing process the materials (eventually virgin material as well - useful f.e. in case of grey materials which may contain dust) get cleaned by being the dust extracted and separated. Dust is then compacted by using a large variety of Hydraulic Dust Compactors.
Third Step: Mixing to virgin beads
For feeding back the block mould or the shape mould with mixed virgin and recycled materials
Mixing Units can be provided based on
- Archimedean Screws ensuring a continuous flow and therefore a well-mixed material (Nip preferred solution); eventually available with more than 2 Archimedean Screws and up to 5 together for mixing as well white & grey virgin materials + scraps from white, grey and “dalmatian” (mixed white & grey) for such special application (dalmatian eps)
- Rotary Sector Valves
Both controlling the revolution speed by inverters in order to adjust the %’s of the different materials and suitable to be integrated eventually in the block mould supervision recipe system
Are available
- Pre-crushers:
- Max scrap thickness 500 ÷ 600 mm (20 ÷ 24 in)
- Sieve diameter 80 mm (3.15 in)
- Productivity:
- type A 25 ÷ 35 m³/h (880 ÷ 1,240 ft³/h)
- type B 32 ÷ 45 m³/h (1,130 ÷1,589 ft³/h)
- Grinders:
- Max scrap thickness 120 ÷ 150 mm (4.7 ÷ 5.9 in)
- Sieve diameter 15 ÷ 30 mm (0.59 ÷ 1.18 in)
- Productivity:
- type A0 10 ÷ 15 m³/h (353 ÷ 530 ft³/h)
- type A 15 ÷ 20 m³/h (530 ÷ 880 ft³/h)
- type B 20 ÷ 30 m³/h (706 ÷ 1,059 ft³/h)
- Grinding Fans after the Grinders:
- Sieve diameter 15 ÷ 6 mm (0.59 ÷ 0.24 in)
- Productivity:
- type A suitable for Grinder type A0
- type B suitable for Grinder -> A & B (in function of sieve diameter)
- Dedusting Plants - Standalone Machines:
- Single:
- type A0 productivity 15 ÷ 16 m³/h (530 ÷ 565 ft³/h)
- type A productivity 35 ÷ 40 m³/h (1,236 ÷ 1,412 ft³/h)
- type B productivity 45 ÷ 50 m³/h (1,589 ÷ 1,766 ft³/h)
- Double:
- type D productivity 110 ÷ 120 m³/h (3,884 ÷ 4,238 ft³/h)
- Single:
- Hydraulic Dust Compactors:
- High Density at output between 300 ÷ 500 g/l (18.7 ÷ 31.2 lb/ft³)
- Only for Dust:
- type A productivity 0,58 m³/h (20.5 ft³/h) compacted material Ø 60 mm (2.36 in)
- type B productivity 0,82 m³/h (29 ft³/h) compacted material Ø 65 mm (2.56 in)
- type C productivity 1,80 m³/h (64 ft³/h) compacted material Ø 70 mm (2.75 in)
- Both for Dust and Scraps:
- type C+ productivity 3,0 m³/h (106 ft³/h) compacted material Ø 75 mm (2.95 in)
- type D productivity 4,5 m³/h (159 ft³/h) compacted material section size 135 x 250 mm (5.31 x 9.84 in)
- type E productivity 15,0 m³/h (530 ft³/h) compacted material section size 215 x 350 mm (8.46 x 13.78 in)